スリップ・ステイックとオーバーラン
ツールのオーバーラン
ボルト/ナットの締結技術で最も重要な目標とされるのは、どのようにして正確なトルクで、そのトルクが再現されてボルトジョイントが締め付けられているかということです。
この目標の最大の障害となるのが慣性です。 回転体は回転を続けようとしますが、その回転体が停止するためには停止時間が必要であり、その時間は回転体のエネルギー量により決定されます。 この停止時間がオーバーラン量になり、これがトルクのバラ付きになりオーバーロードの原因となります。
回転体のエネルギー量は
Erot = J * ω2/2
J = m * d2 (回転体の慣性モーメント)
あるいは
Erot = m * d2 * ω2/2
Erot: 回転エネルギー
J : 慣性モーメント
ω : 角速度
m : 質量
d : ローター直径
公式から、回転エネルギーは質量、ローター直径の二乗、角速度の二乗に比例することがわかります。 つまり、締付ツールの駆動装置は、軽く、ローター直径が小さいものが理想的となります。
一方、角速度はエネルギー量に二乗で貢献しています。 つまり、できるだけ角速度(回転数)遅くすると回転エネルギーも小さくできます。
現在は製造時間をできるだけ短縮するためにツーステップ締め付けが一般的に採用されています。 一段目を早い回転で予備締め付け、その後短い停止時間後、遅い回転で目標トルクまで締め付ける方法です。 適切な締め付けを行うためには、一段目のオーバーラン量を正しく判定し、一段目の切り替え目標トルクを適切に設定されなければなりません。
モータータイプ
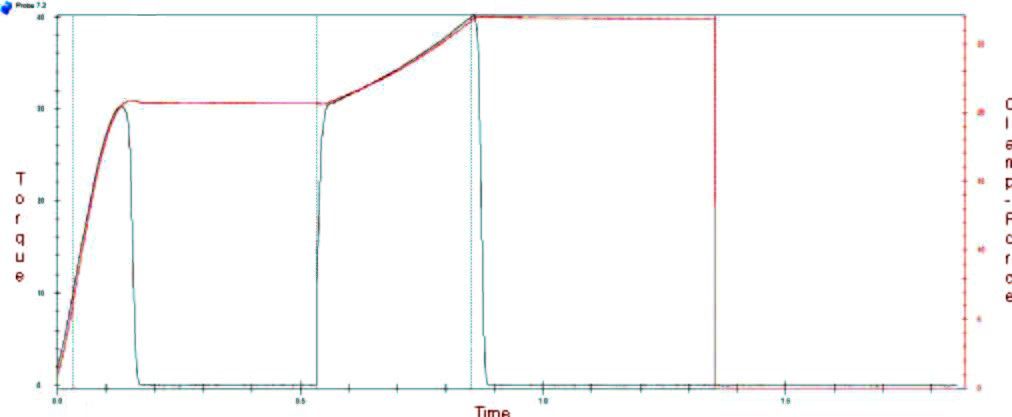
(Motor 2)を使用して、典型的なオーバーランの実験計測トルク/カーブです。
モーターのサーボレギュレーターをオフにしブレーキシステムを無効に設定し、ブレーキ力は締付で上昇するトルクとギアボックスの摩擦抵抗だけに装置は設定されています。
一段目の締め付けは200rpm目標トルクは10Nm、停止時間0.5秒、その後、速度20rpm目標トルク40Nmに設定されています。
結果
一段目締め付けのオーバーラン量は、30.3Nmと300%以上、二段目は40.23Nmと目標トルクに対し、許容限界内の結果になりました。
この締め付けで、目標トルクが30Nmであったならば、一段目のオーバートルクで終了してしまいます。
異なった3タイプモーターのオーバーランいついて考察します。
ブレーキシステムは有効にされ、目標トルクも2Nmと低く設定し、カットオフ時の回転速度をモータースペックに近くなるようにした実験です。
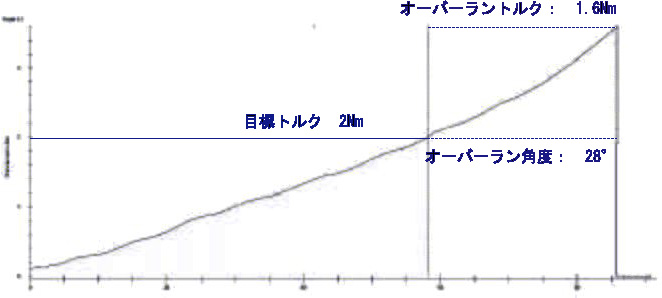
(Motor 1)を使い、目標トルク2Nm、締め付け速度150rpmで締め付け時のオーバーラン量の測定グラフ
オーバートルク量: 1.6Nm(80%オーバートルク)
オーバーラン角度28°
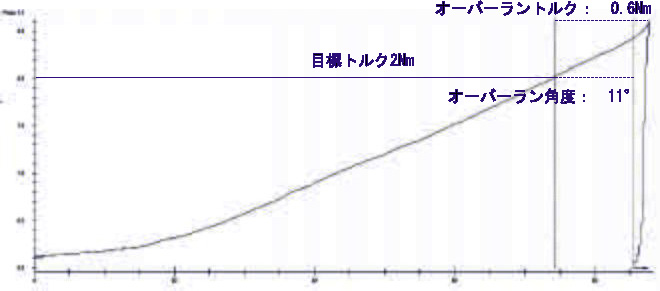
(Motor 2)を使い、目標トルク2Nm、締め付け速度200rpmで締め付け時のオーバーラン量の測定グラフ
オーバートルク量: 0.6Nm(30%オーバートルク)
オーバーラン角度11°
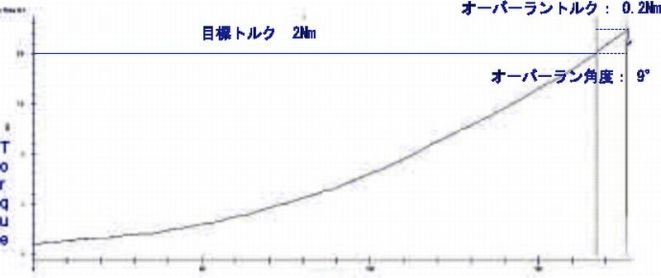
(Motor 3)を使い、目標トルク2Nm、締め付け速度200rpmで締め付け時のオーバーラン量の測定グラフ
オーバートルク量: 0.2Nm(12%オーバートルク)
オーバーラン角度9°
他方、モーターは細いスピンドルタイプと言われる締め付けドライブ装置が使われ、細いモーター駆動軸になったことにより、スリップ・スティック現象の発生が問題になってきます。
スリップ・ステイック現象
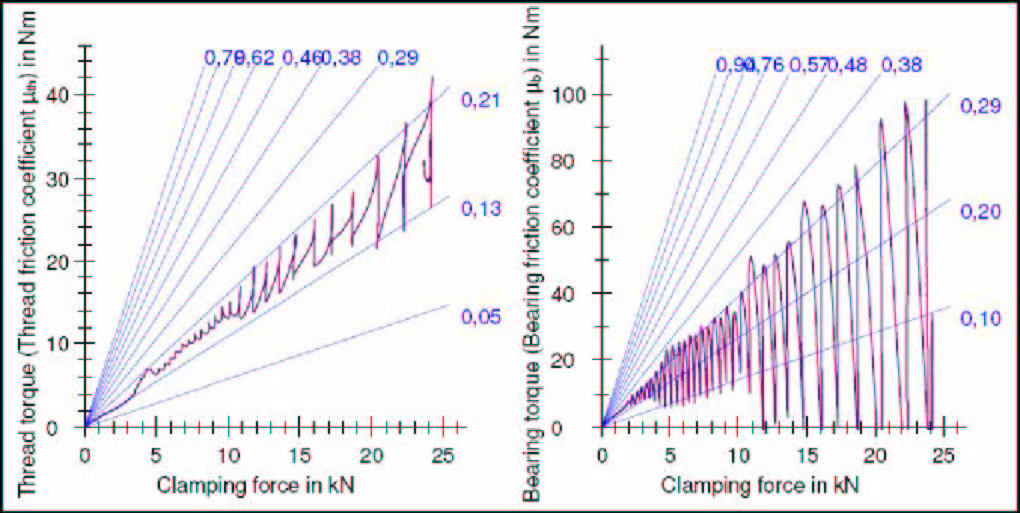
しかし、ボルト、あるいはナットが止まったとしても工具のシャフトは回転し続け、トルクがブレークウェイトルクに達して再度ボルトあるいはナットが動き始めます。 このモーターシャフトのねじれのスプリングのようなパルスエネルギーはボルトあるいはナットが動くと瞬間的に開放され、ボルトあるいはナットは再び止まってしまいます。 この一連の現象がツールのカットオフまで連続して起こるのが「スリップ・ステイック」現象です。
モーター駆動軸の捻れによるスプリング力が発生する場合に発生する現象ですが、絶対条件として摩擦係数がμ=0.2以上であることです。
スリップ・ステイック現象を防ぐために太い駆動軸の大きいモーターを使用すればモーター軸の捻れが少なく発生しませんが、新しいコーティングや新しいボルト/ナットを試験する時は、VDA235−203は実際に組み立てラインで使用される細い駆動軸のモーターのナットランナーを使用することを規定しています。
スリップ・スティック現象が実際の製造ラインで起こしてはならない理由
製造ラインでは、センサー組み込みのナットランナーが使用されていますが、それはピークトルク値のみを表示します。
1. トルクコントロール法
この締め付け方法は、設定トルクで工具はシャットオフされる方法です。 しかし、スリップ・スティック現象が発生する
と、トルクのピーク値(静的トルク=ブレークアウェイトルク)が設定トルク以上を示して停止します。 この時点では、軸
力は目標トルクには程遠い締付で終了してNOK締め付けになります。
2. アングルコントロール法
スリップ・スティック現象が角度計測開始トルク以降に発生した場合は、角度は正しく計測され設定角度まで締め付け
は進行します。 しかし、トルク値は、常にトルク上限値より高くなります。
しかし、より頻度の高いのはスリップ・ステイック現象が角度計測開始トルク以前に発生し、それにより早過ぎる角度計
測が開始され設定角度よりかなり少ない角度を誤認して締め付けが終了し、NOK締付になります。
3. 降伏点コントロール法
トルク係数をモニターすることで締め付け制御する方法です。 そのため、トルクは一定に増加する必要があります。
しかし、スリップ・スティック現象が発生すると、この方法では降伏点が正しく認識されません。
KRE®Analyse Vertical system
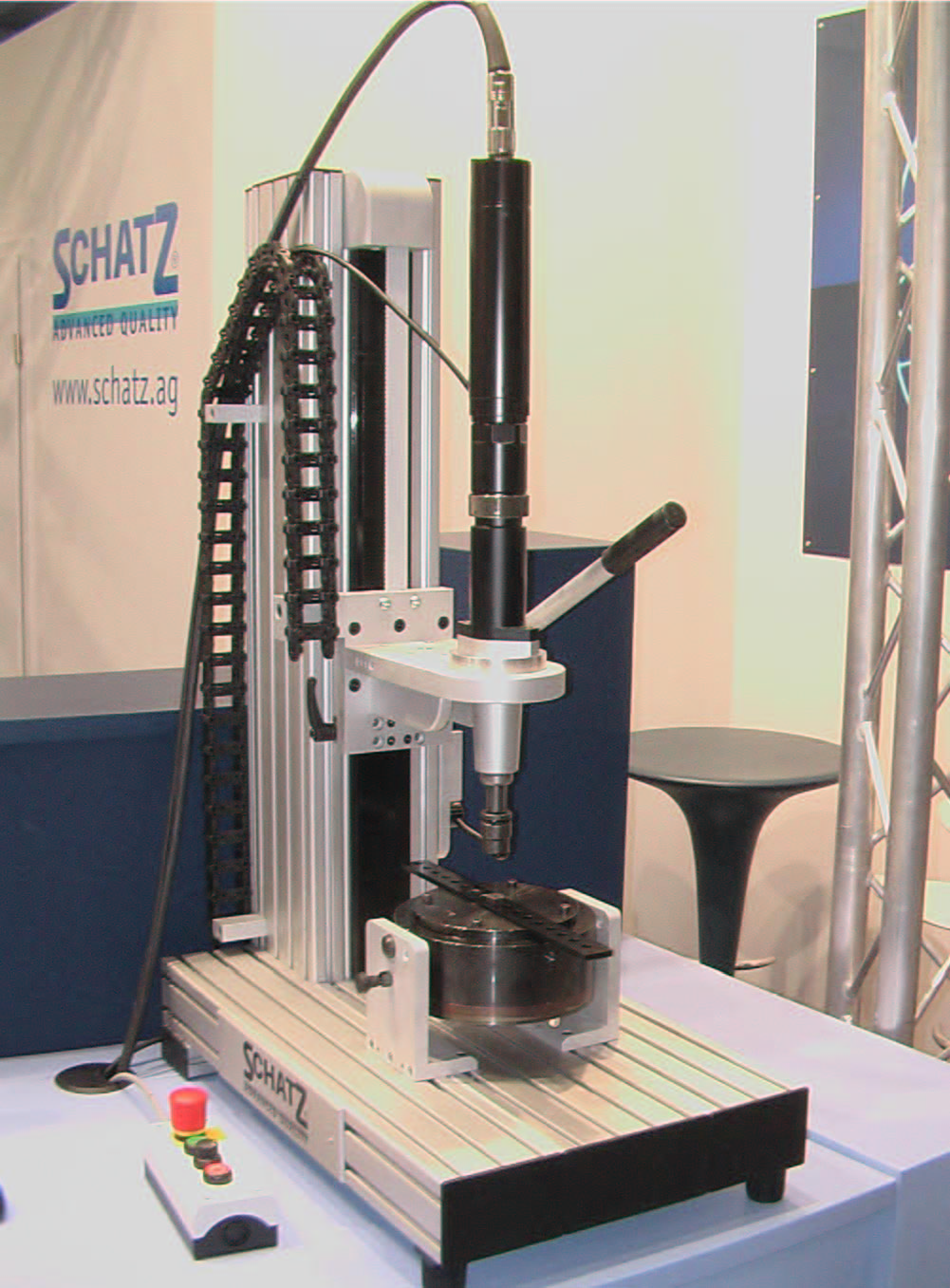
KREが、このシステムに提供できるスピンドル
a) 最大トルク/速度 200Nm/360rpm;M4-M12(class 12.9)
b) 最大トルク/速度 300Nm/400rpm;M12-M16(class 10.9)
c) 最大トルク/速度 400Nm/300rpm;M14-M18(class 8.8)
d) 最大トルク/速度 500Nm/200rpm;M14-M20(class 8.8)
b) - d)のスピンドルの直径は同じです。
Boschの下記のスピンドルも使用できます。
e) 最大トルク/速度 12 Nm/1000rpm;M4-M6(class 8.8)
f) 最大トルク/速度 60 Nm/ 530rpm;M6-M10(class 8.8)
g) 最大トルク/速度 165 Nm/ 340rpm;M8-M12(class 12.9)
h) 最大トルク/速度 460 Nm/ 147rpm;M12-M18(class10.9)
これらのスピンドルは、KRE®AnalyseパワーパックM/N2777 P2でサーボコントロールされます。
スリップ・スティック現象の実証試験には、目標トルクに対しできるだけ小さいスピンドルを選択します。